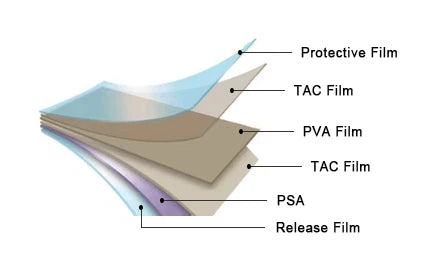
Basic Structure of Polarizers

Polarizers are optical components made up of multiple composite layers. From top to bottom, these layers are the protective film, TAC layer, PVA layer, TAC layer, PSA layer, and release film.
PVA Layer
The PVA (polyvinyl alcohol) layer is the core part of the polarizer that achieves the polarization effect. It is about 20µm thick. Iodine ions in the PVA absorb one polarization state of natural light and transmit the other, thus producing polarized light.
TAC Layer
The TAC (Tri-Acetate Cellulose) layer mainly supports and protects the PVA layer. Common thicknesses are 40µm and 60µm. PVA films are weak, brittle, and highly hydrophilic, making them prone to shrinking, deforming, and fading in humid and hot environments. Therefore, protective materials are added on both sides. TAC, made of triacetate cellulose ester, has high strength, heat resistance, and high transmittance, making it a common protective material for the PVA layer.
NRT (No Retardation TAC) is a type of TAC film with no optical delay, achieved by improving the stretching process, which helps reduce light leakage in dark states. NRT is often used to replace the TAC layer closer to the glass side.
Although TAC has many advantages, its high water absorption rate can cause deformation in high-temperature and humid environments or over long storage periods, leading to display issues like light leakage or wrinkling. To address these problems, alternative materials such as Poly Methyl Methacrylate (PMMA, also known as acrylic), Polyethylene Terephthalate (PET), and Cyclic Olefin Polymer (COP) have been developed. These materials have lower water absorption rates, reducing the risk of light leakage caused by expansion. COP, with a low photoelastic coefficient (about one-tenth that of TAC), is beneficial for reducing light leakage due to internal stress. However, PMMA and COP also have drawbacks in practical applications. Polarizers using PMMA may show a blue tint or other Mura defects in dark states, and COP is soft, requiring protective cover glass when used on the color filter side. COP is commonly used to replace the TAC material under the PVA layer. Additionally, when both the upper and lower TAC layers of a polarizer are replaced with COP, UV glue is needed to bond the PVA and COP layers because the low water absorption rate of COP makes it difficult for conventional water-based adhesives to dehydrate and cure.
PSA Layer
The PSA (Pressure Sensitive Adhesive) layer is a pressure-sensitive adhesive, about 20µm thick, that adheres to surfaces through pressure. Its role in the polarizer is to ensure reliable attachment to the glass substrate. It also has good resistance to humidity and heat and can be re-peeled.
Release Film and Protective Film
The release film and protective film protect the polarizer during storage and transportation. They protect the PSA and TAC layers, respectively, and are usually made of PET.
Compensation Film
Since liquid crystal molecules are rod-shaped, the phase difference of incident light in the long-axis and short-axis directions can cause contrast and color deviations, resulting in color shifts and uneven brightness at different viewing angles. Therefore, compensation films, which provide polarization compensation, are often added to polarizers to partially correct phase differences at different viewing angles and improve image quality. Compensation films are generally made of cured polymer liquid crystal (e.g., cholesteric liquid crystal) films. For VA or TN mode polarizers, compensation films primarily improve viewing angle characteristics, while for IPS and FFS (ADS) mode polarizers, they mainly address color shifts and dark state light leakage. Additionally, to enhance the transmittance of LCDs, polarizers may incorporate brightness-enhancing films, increasing transmittance by about 30%.