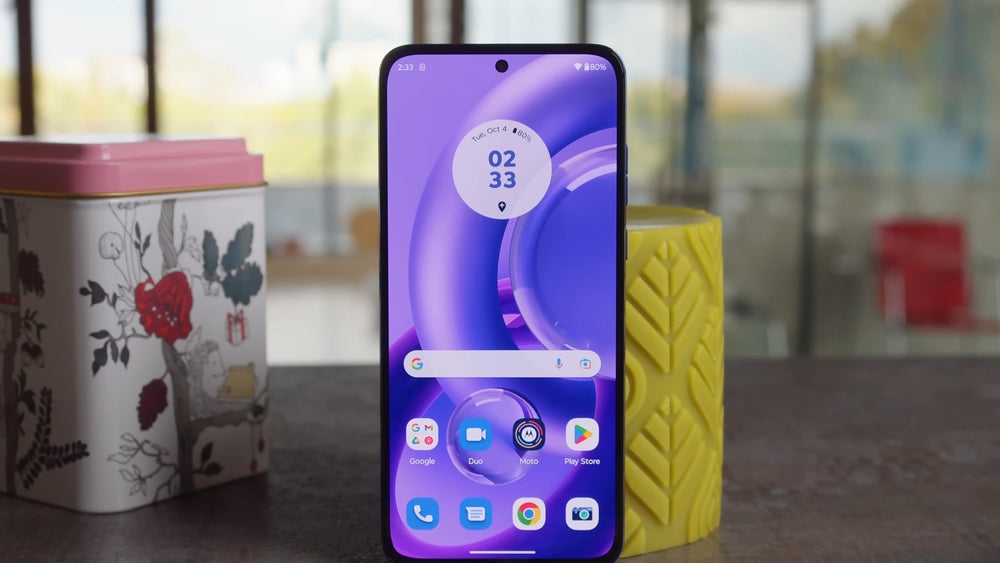
Composition of the Display: Sealing Area
The sealing area in a liquid crystal display (LCD) is the region extending from the boundary of the active display area to either the pad area or the cutting edge of the glass substrate. This area plays a crucial role in sealing both the liquid crystals inside the display and the light from the backlight source.
Functions of the Sealing Area
1. Sealing the Liquid Crystals:
• Preventing Leakage: To prevent the liquid crystals from leaking out of the display, a sealant is applied around the periphery of the display. This sealant also adheres the color filter substrate to the array substrate.
• Structural Support: The sealant contains silica or plastic spheres that help maintain the uniform thickness of the liquid crystal cell, ensuring consistent display performance.
• Electrical Connectivity: For larger displays using TN or VA modes, the sealant often includes conductive gold balls to connect the top and bottom glass substrates. In smaller displays, this connection might be achieved using silver paste applied at the corners of the liquid crystal cell.
2. Light Sealing from the Backlight:
• Preventing Light Leakage: The sealing area also helps prevent light from the backlight from leaking out of the non-display area. This is achieved using a black matrix (BM) on the color filter substrate, which blocks light in the sealing area.
Sealing Process
• UV Curing: After aligning the array and color filter substrates in a vacuum environment, the sealant is immediately cured using ultraviolet (UV) light to prevent contamination or leakage of the liquid crystals. The direction of UV exposure can vary:
• From the Color Filter Substrate Side: The BM edges and the sealant edges must maintain a gap to allow sufficient UV exposure. This gap accounts for the tolerances in sealant application and spreading, as well as a safety margin.
• From the Array Substrate Side: The metal patterns on the array substrate must allow enough light to pass through (typically more than 40% transparency) and avoid wide lines or shapes that could block the UV light. This method generally requires the sealing area to be larger compared to exposure from the color filter side, making it suitable for products with narrow bezels. However, this also increases the design complexity of the array patterns, potentially leading to higher resistance in the lines and increased load on the driving signals.
Considerations for Design
• UV Exposure Direction: The direction from which UV light is applied affects the width of the BM in the sealing area. For narrow bezel designs, exposure from the array substrate side is preferred but requires careful design to ensure adequate UV curing.
• Precision and Tolerances: Ensuring the sealant is exposed adequately to UV light while maintaining the necessary tolerances for sealant application and BM design is critical. The design must balance between sufficient sealant exposure for effective curing and maintaining electrical and optical performance.